Metal Stamping Defects
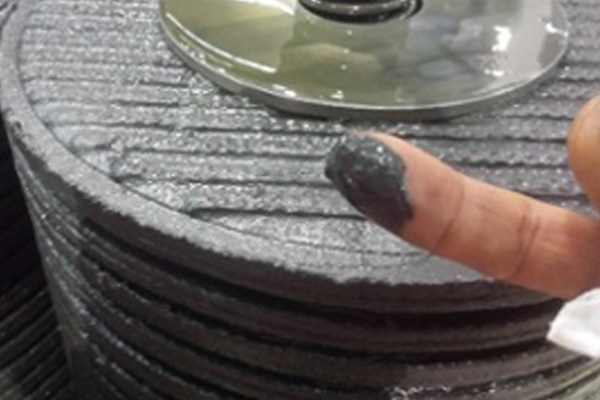
Metal Stamping Defects
Find out how we helped an automotive stamping plant eliminate the production of defective parts with surface imperfections resulting from highly contaminated lube oil.
An automotive stamping plant operating large presses to produce body panels was experiencing high surface finish defect scrap. Lubricating oil contamination was causing surface imperfections that would be visible after painting.
The uncoiler / washer lube oil system was protected by an offline filtration system fitted with stacked disc cellulose media filter inserts (elements). Oil analysis revealed an operating ISO code of 23/19/11. Patch analysis showed cellulose fibers were shedding into the oil from the filter inserts downstream of the filtration system.
Our experts assessed the situation, and recommended a full system clean-out, lower operating ISO codes, and eliminating cellulose fiber shedding ingression to eliminate defects. The lube oil was transferred to a clean storage tote using a Hy-Pro FCL10 off-line filter cart with 6M (β7[c] > 1000) media element and recirculated to reach an ISO code of 17/13/11. The reservoir, existing off-line filter assembly, and sieve were then cleaned—revealing a high volume of sediment and cellulose fibers. The offline filter systems cellulose stacked disc elements were upgraded to Hy-Pro HP2727L43-6MB pleated glass elements (β7[c] > 1000). Finally, the fluid was returned to the system.
In less than three weeks, the operating ISO code had decreased further to 17/13/9, eliminating all defects and restoring optimal performance. To verify the results, the stamping plant put another set of the original stacked disc filters back in the off-line filter system and within 15 days the operating ISO code was 23/19/11 again.
Along with longer filter element life and the useful oil life, our services saved the stamping plant hundreds of thousands of dollars per year.